
Outdoors. Indoors. Sitting, or hanging. A lamp for any use. Anywhere.
Whether in the living room or out at the campgrounds, light can bring life to the spaces that we call home. By providing an ambient illumination, from either above or below, Luma invites us to come together even in the most inconvenient of places.

Inspiration
For this project, I was inspired by the utilitarian minimalism of many products currently on the market. I wanted the physical realities of production (such as seams, buttons, etc) to be integrated into the design itself, rather than obfuscated.
Features
Collapsible hidden strap
Easy-access battery
Soft ambient glow
Developing a form both interesting and usable.
Initial concepts exploring free-form curves and organic shapes
Experiments with relationship between curved and straight edges
Design focus narrowed on purely geometric forms with attached strap
Refined explorations of strap attachment and part assembly
Working in 3D space
Several design ideas were brought forward into the 3D stage. By doing so, multiple viable designs could be developed and tested in tandem before deciding which held the most merit.
Low-fidelity models
Fast models were made from foam to quickly transfer the concepts into physical form. By doing so, it became clearer how these design might appear from multiple angles.
CAD development
As the project moved closer toward prototyping, several of my concepts were built out in Fusion360. The move to 3D software gave me the ability to experiment faster with the finer details, such as edge bevels and to see how that affected the overall aesthetic.
Additionally, the logistics of how the form would house the necessary internal components also began development.

Prototyping and Testing
Once completed, the files were prepped and then sent over for 3D printing, Physical models were then promptly used to test various aspects of design, such as light transmission, connection points, tolerances, and overall functionality.
Through this process, various strap attachments were tested, revealing what worked and what didn’t. After much iteration, it became apparent that the design would need to allow the strap to be covertly stored in the base (as to not hinder stability when used flat on the table).
Assembly tolerance
Light transmission
Test analysis and conclusions
The rapid prototyping tests provided valuable information on the current issues with my design and how best to proceed with revisions.
Considerations for my final iterations included:
1. Redesigning assembly parts for easier mass production
2. Reworking strap attachments to not hinder design when not in use
3. Modifying assembly connections and tolerances for better fit/ ease of use.
4. Making battery pack accessible without complex disassembly
5. Tweaking wall thickness for better light transmission
Initial Construction
Revised Design
Final prototype
Printing and Sanding
When all necessary changes were made in Fusion 360 and the design was ready for a final prototype, it was printed out on a Bambu printer, cleaned of all supports , and then sanded to smooth finish in preparation for painting.
Materials
The final parts were covered with masking tape in areas where paint wasn’t wanted.
Primer was then applied to the base sections to render them opaque.
Lastly, several sprays were applied resembling the materials that would be used in the final product, such as dark metal and chrome.
Assembly
The printed pieces were finally assembled, one piece at a time. Because of imperfections inherent to 3D printing, it was crucial to test all moving parts and mechanism to make sure that they would work reliably and not stick. Any trouble spots were further sanded to increase tolerance and reduce friction.
Fully Functional Prototype

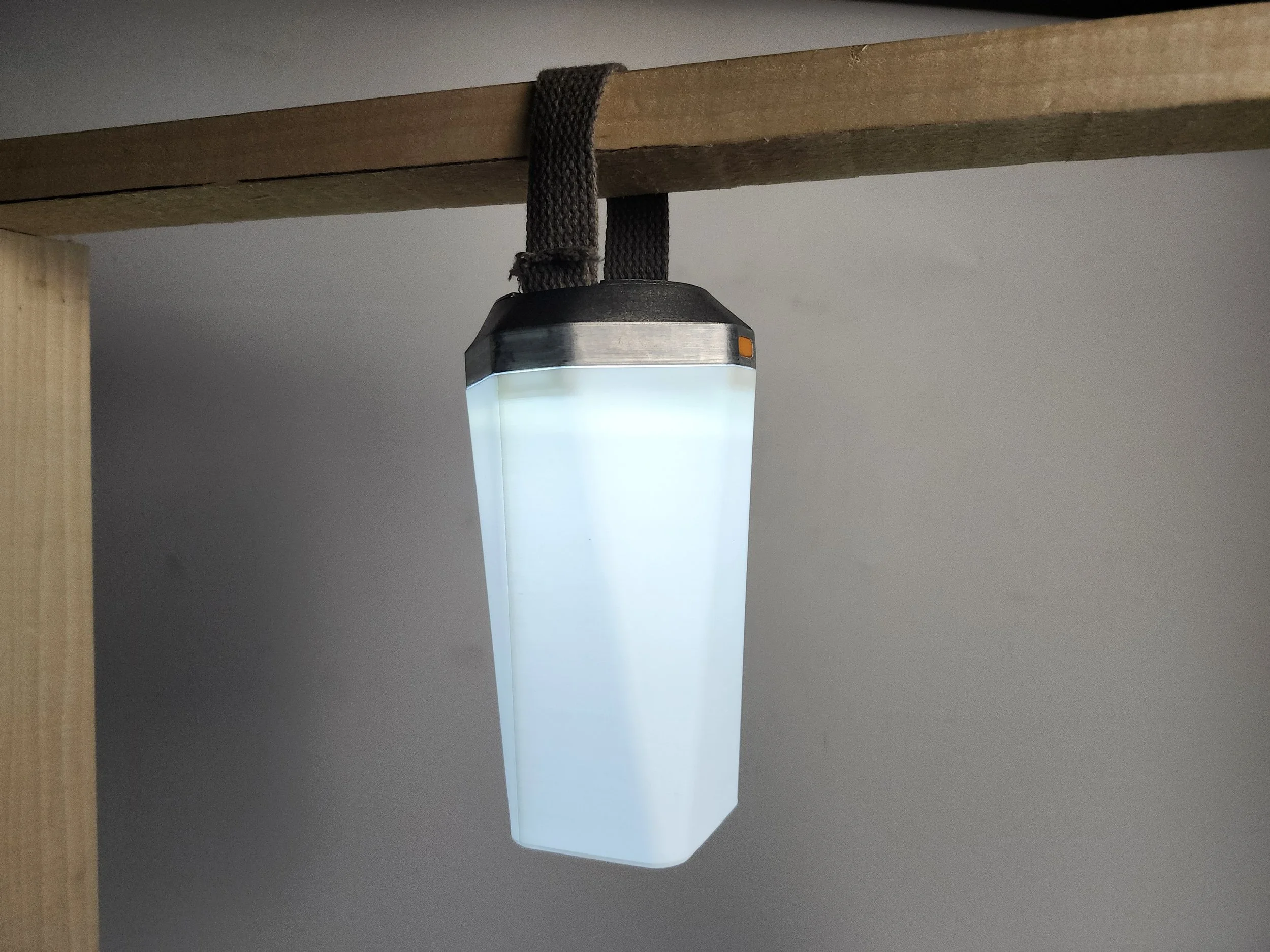

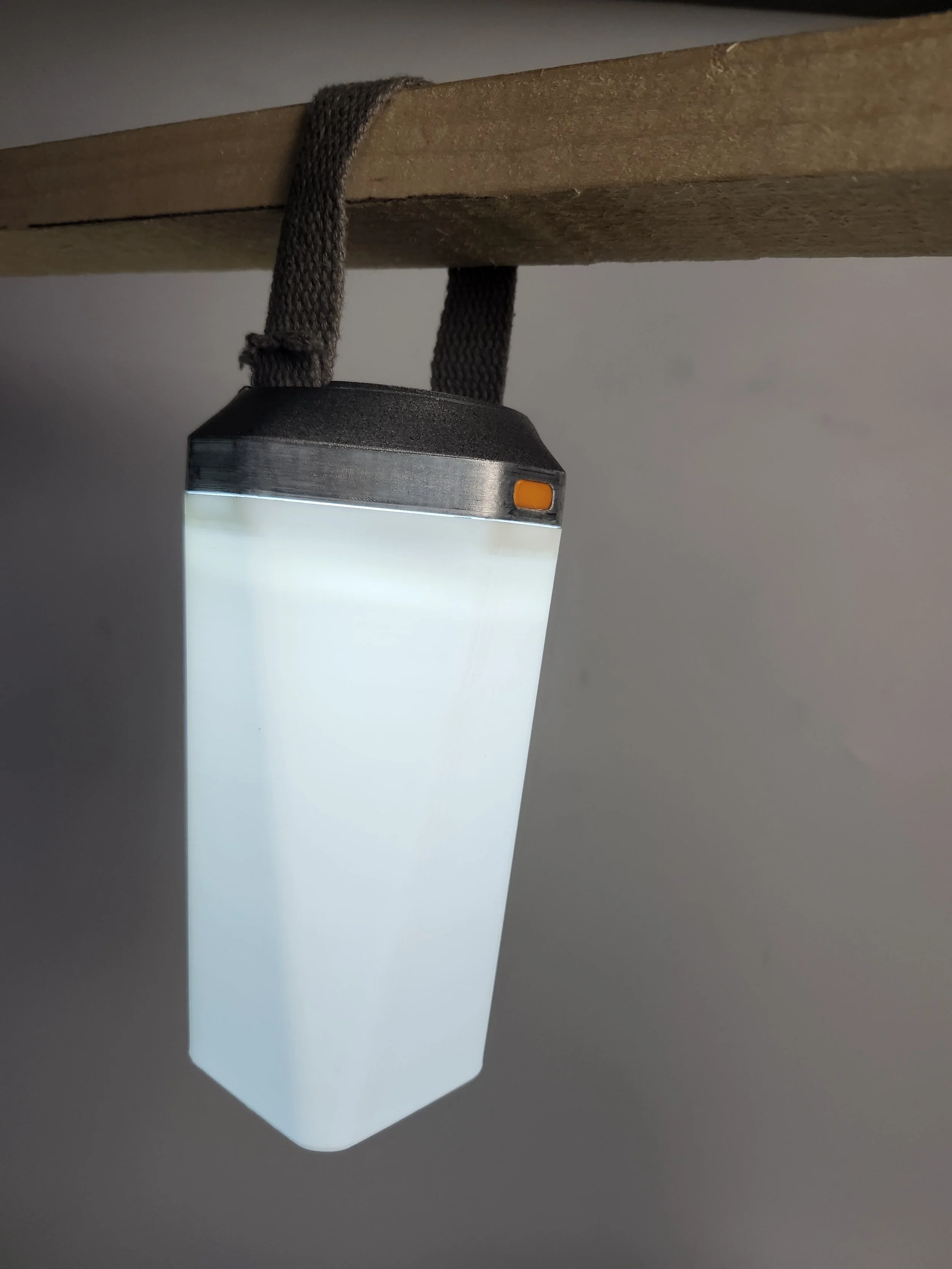
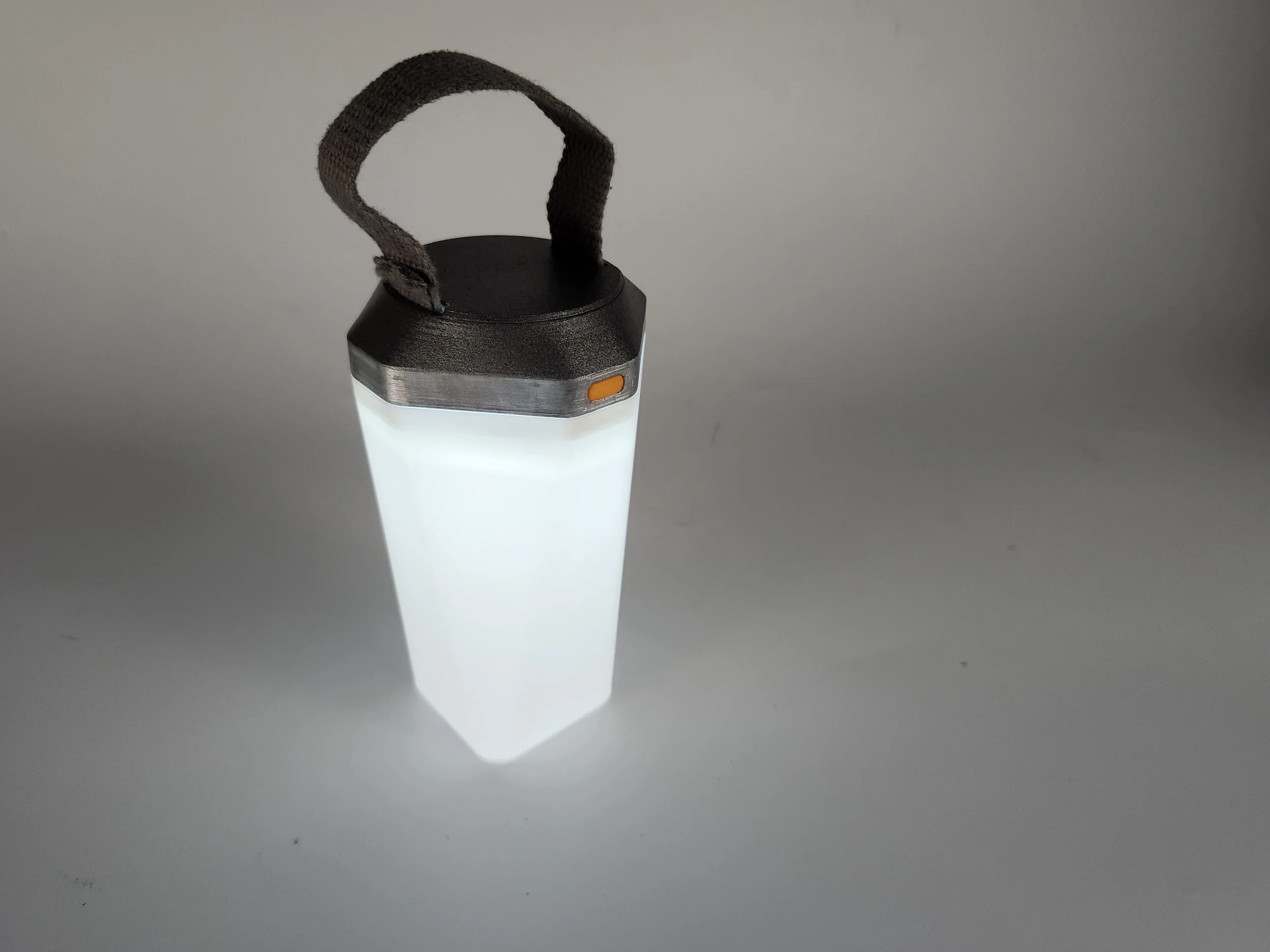